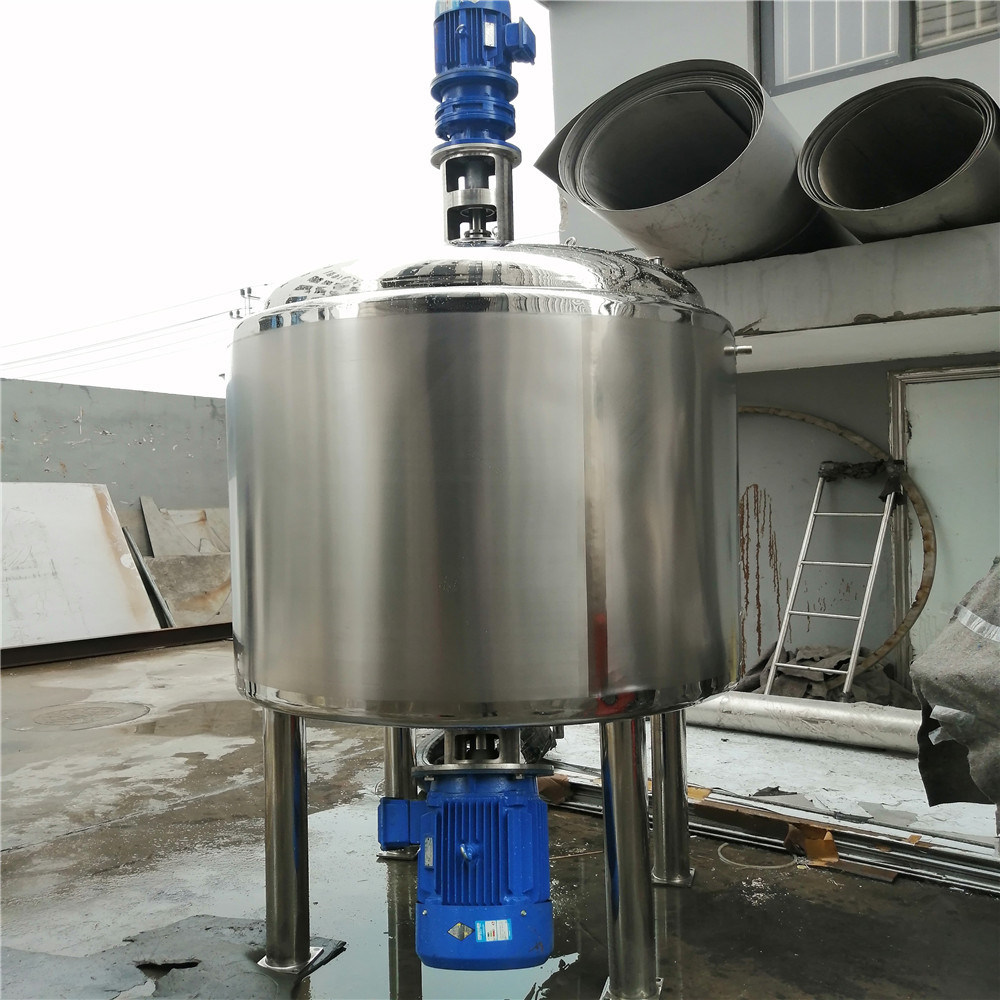
Cuves et conteneurs de mélange industriels : optimiser la manipulation des liquides dans l'industrie
Les réservoirs et conteneurs de mélange industriels sont des composants importants dans divers processus de fabrication, réactions chimiques et systèmes de stockage de matériaux. Ces réservoirs sont conçus pour traiter une large gamme de liquides, de produits chimiques et de boues, offrant ainsi un mélange et un stockage efficaces. Dans cet article, nous examinerons les différents types de cuves et de conteneurs de mélange industriels, leurs fonctionnalités et leurs applications dans diverses industries.
1. Réservoirs de stockage :
Les réservoirs de stockage sont utilisés pour stocker des liquides, des produits chimiques et des matières premières dans des installations industrielles telles que les raffineries de pétrole, les usines chimiques et les usines de fabrication. Ces réservoirs sont disponibles dans une variété de tailles, de formes et de matériaux pour répondre à différentes exigences de stockage et conditions environnementales. Les principales caractéristiques et avantages des réservoirs de stockage sont les suivants :
- Compatibilité des matériaux : les réservoirs de stockage sont fabriqués à partir de matériaux tels que l'acier inoxydable, l'acier au carbone, la fibre de verre et le polyéthylène, offrant une compatibilité avec une large gamme de liquides et de produits chimiques.
- Conception personnalisable : les réservoirs de stockage peuvent être équipés de fonctionnalités telles qu'une isolation, des enveloppes de chauffage/refroidissement, des systèmes d'agitation et des capteurs de niveau pour répondre à des besoins spécifiques de stockage et de traitement.
- Conformité en matière de sécurité : les réservoirs de stockage sont conçus et fabriqués conformément aux normes et réglementations de l'industrie, y compris des fonctionnalités telles que les systèmes de ventilation, la protection contre le débordement et l'étanchéité secondaire pour garantir la sécurité environnementale.
- Applications polyvalentes : les réservoirs de stockage sont utilisés dans des secteurs tels que le pétrole et le gaz, les produits pharmaceutiques, l'agroalimentaire et le traitement de l'eau pour stocker des liquides, des produits intermédiaires et des produits finis en vrac.{28 }
2. Réacteurs :
Les réacteurs sont des récipients utilisés pour effectuer des réactions chimiques, mélanger des réactifs et produire les produits souhaités dans les industries chimique, pharmaceutique et pétrochimique. Ces conteneurs sont conçus pour résister aux températures élevées, aux pressions et aux environnements corrosifs créés lors des réactions chimiques. Les principales caractéristiques et avantages des réacteurs incluent :
- Contrôle de la réaction : les réacteurs sont équipés de fonctionnalités telles que des systèmes d'agitation, des enveloppes de chauffage/refroidissement et des capteurs de température/pression pour surveiller les paramètres de réaction et optimiser la qualité et le rendement du produit.
- Fonctionnement par lots et continu : les réacteurs peuvent être exploités en mode par lots pour la production à petite échelle ou en mode continu pour les applications de traitement continu à grande échelle, offrant ainsi une flexibilité et une production évolutive.
- Sélection des matériaux : les réacteurs sont fabriqués à partir de matériaux tels que l'acier revêtu de verre, l'acier inoxydable et des alliages exotiques qui peuvent résister aux produits chimiques agressifs, aux températures élevées et aux contraintes mécaniques rencontrées lors des réactions chimiques.
- Intégration des processus : les réacteurs peuvent être intégrés à d'autres équipements de processus tels que des pompes, des échangeurs de chaleur et des systèmes de filtration pour créer des lignes de processus intégrées pour un traitement et une production chimiques efficaces.
3. Appareils à pression :
Les récipients sous pression sont conçus pour stocker des liquides ou des gaz à une pression sensiblement différente de la pression ambiante, généralement une pression plus élevée. Ces réservoirs sont utilisés dans des industries telles que le pétrole et le gaz, le traitement chimique et la production d'électricité pour stocker, transporter et traiter des gaz et des liquides comprimés. Les principales caractéristiques et avantages des appareils sous pression sont les suivants :
- Normes de sécurité : Les appareils sous pression sont conçus, fabriqués et testés conformément aux normes et codes rigoureux de l'industrie, tels que le code ASME sur les chaudières et les appareils sous pression, pour garantir un fonctionnement sûr et fiable.
- Décharge de pression : les récipients sous pression sont équipés de dispositifs de décompression, tels que des soupapes de surpression, des disques de rupture et des régulateurs de pression, pour éviter la surpression et garantir un fonctionnement sûr.
- Résistance des matériaux : Les récipients sous pression sont fabriqués à partir de matériaux tels que l'acier au carbone, l'acier inoxydable et les alliages d'aluminium, dotés d'une résistance à la traction et d'une ténacité élevées pour résister aux charges de pression internes et aux conditions environnementales externes.{ 72}
- Diverses applications : Les appareils à pression sont utilisés dans des industries telles que la chimie, le raffinage du pétrole, le traitement de l'eau et l'aérospatiale pour stocker et traiter des gaz, des liquides et des produits chimiques comprimés.
Conclusion :
Lesréservoirs industriels et conteneurs jouent un rôle essentiel dans l'optimisation des opérations de manipulation de liquides dans divers secteurs. Qu'il s'agisse de stocker des matières premières, de réaliser des réactions chimiques ou de manipuler des liquides sous pression, ces récipients sont des éléments importants des processus industriels modernes. En tirant parti des capacités et des avantages des réservoirs de stockage, des réacteurs et des récipients sous pression, les installations industrielles peuvent améliorer l'efficacité de la production, garantir la qualité des produits et répondre à des exigences réglementaires strictes dans un large éventail d'applications. Grâce aux progrès continus dans les technologies de conception, de matériaux et de contrôle des processus, les cuves et cuves de mélange industrielles continuent de stimuler l'innovation et le progrès dans le paysage industriel mondial.