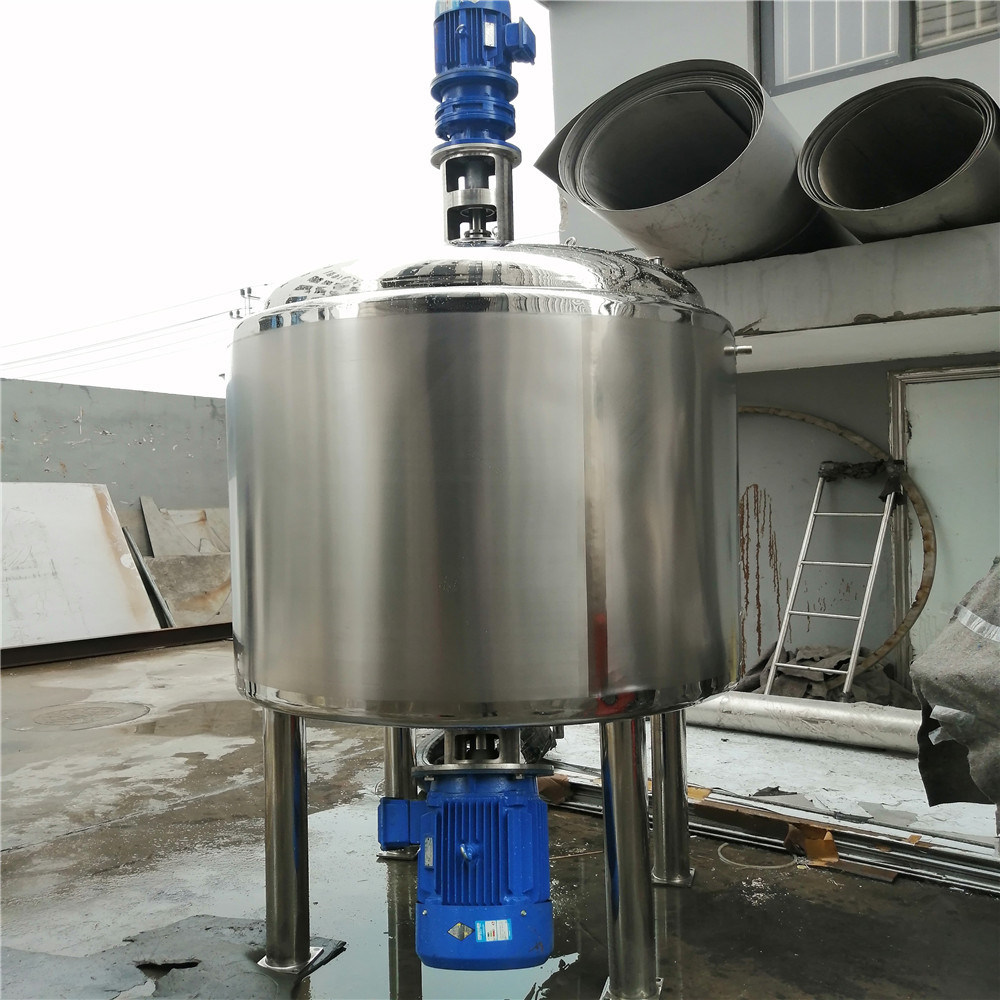
Industrial mixing tanks and containers: optimizing liquid handling in industry
Industrial mixing tanks and containers are important components in various manufacturing processes, chemical reactions and material storage systems. These tanks are designed to handle a wide range of liquids, chemicals and slurries, providing efficient mixing and storage. In this article, we will look at the different types of industrial mixing tanks and containers, their functionality and applications in various industries.
1. Storage Tanks:
Storage tanks are used to store liquids, chemicals and raw materials in industrial facilities such as oil refineries, chemical plants and manufacturing plants. These tanks come in a variety of sizes, shapes and materials to suit different storage requirements and environmental conditions. Key features and benefits of storage tanks include:
- Material Compatibility: Storage tanks are made from materials such as stainless steel, carbon steel, fiberglass and polyethylene, providing compatibility with a wide range of liquids and chemicals.
- Customizable Design: Storage tanks can be equipped with features such as insulation, heating/cooling jackets, agitation systems and level sensors to suit specific storage and processing needs.
- Safety Compliance: Storage tanks are designed and manufactured to industry standards and regulations, including features such as ventilation systems, overfill protection and secondary sealing to ensure environmental safety.
- Versatile Applications: Storage tanks are used in industries such as oil and gas, pharmaceutical, food and beverage, and water treatment to store liquids, intermediates, and bulk finished products.{28 }
2. Reactors:
Reactors are vessels used to carry out chemical reactions, mix reactants and produce desired products in the chemical, pharmaceutical and petrochemical industries. These containers are designed to withstand high temperatures, pressures and corrosive environments created during chemical reactions. Key features and benefits of the reactors include:
- Reaction Control: Reactors are equipped with features such as stirring systems, heating/cooling jackets, and temperature/pressure sensors to monitor reaction parameters and optimize product quality and yield.
- Batch and Continuous Operation: Reactors can be operated in batch mode for small-scale production or in continuous mode for large-scale continuous processing applications, providing flexibility and scalable production.
- Material Selection: Reactors are made from materials such as glass-lined steel, stainless steel, and exotic alloys that can withstand harsh chemicals, high temperatures, and mechanical stress encountered during chemical reactions.
- Process Integration: Reactors can be integrated with other process equipment such as pumps, heat exchangers and filtration systems to create integrated process lines for efficient chemical processing and production.
3. Pressure vessels:
Pressure vessels are designed to store liquids or gases at a pressure significantly different from the ambient pressure, usually a higher pressure. These tanks are used in industries such as oil and gas, chemical processing and power generation to store, transport and process compressed gases and liquids. Key features and benefits of pressure vessels include:
- Safety Standards: Pressure vessels are designed, manufactured and tested to stringent industry standards and codes, such as the ASME Boiler and Pressure Vessel Code, to ensure safe and reliable operation.
- Pressure Relief: Pressure vessels are equipped with pressure relief devices, such as relief valves, rupture discs, and pressure regulators, to prevent overpressure and ensure safe operation.
- Material Strength: Pressure vessels are made from materials such as carbon steel, stainless steel and aluminum alloys with high tensile strength and toughness to withstand internal pressure loads and external environmental conditions.{ 72}
- Various Applications: Pressure vessels are used in industries such as chemical, petroleum refining, water treatment and aerospace to store and process compressed gases, liquids and chemicals.
Conclusion:
Industrial tanks and containers play a critical role in optimizing liquid handling operations across a variety of industries. Whether for storing raw materials, carrying out chemical reactions or handling liquids under pressure, these vessels are important components of modern industrial processes. By leveraging the capabilities and benefits of storage tanks, reactors and pressure vessels, industrial plants can improve production efficiency, ensure product quality and meet stringent regulatory requirements in a wide range of applications. Through continuous advancements in design, materials and process control technologies, industrial mixing tanks and vessels continue to drive innovation and progress across the global industrial landscape.