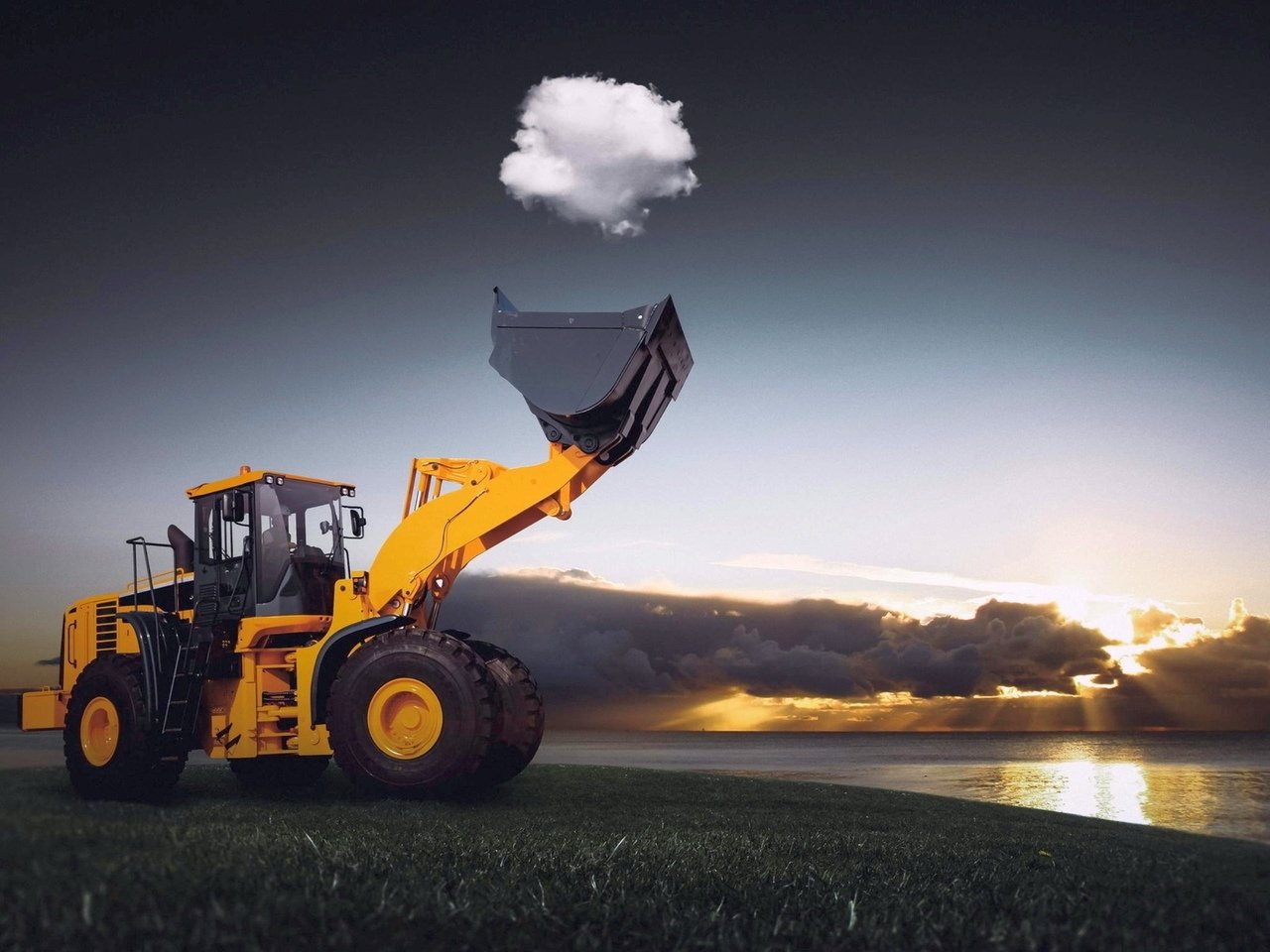
Tips for keeping special equipment in perfect condition
Proper maintenance of specialty equipment is vital to ensure longevity, reliability and safety. Whether you operate construction equipment, farm equipment, or any other specialized equipment, following these maintenance tips will help keep your equipment in optimal condition, preventing costly breakdowns and downtime.
1. Follow manufacturer's recommendations
Always follow the manufacturer's recommended maintenance schedule and guidelines. These important instructions can be found in the equipment owner's manual. These cover maintenance intervals, lubrication points and inspection procedures.
2. Regular checks
Perform regular visual inspections of equipment before each use. Look for signs of wear, loose bolts, leaks and damaged components. Correct any problems promptly to prevent further damage.
3. Fluids and lubricants
Check and maintain proper fluid levels such as engine oil, coolant, hydraulic fluid, and transmission fluid. Make sure lubrication points are properly lubricated according to manufacturer's recommendations.
4. Air filters
Clean or replace air filters regularly to prevent contaminants from entering the engine or hydraulic system. Clogged filters can reduce efficiency and cause engine damage.
5. Fuel system
Keep the fuel system clean and free of contaminants by using clean fuel and replacing fuel filters regularly. Water separators can help remove moisture from fuel.
6. Cooling system
Maintain the cooling system to prevent overheating. Check the radiator fins for dirt and clean them regularly. Ensure that coolant level and quality meet manufacturer specifications.
7. Tire Maintenance
Check tires for wear, damage and proper inflation. Underinflated or damaged tires can affect equipment stability and performance.
8. Electrical system
Check the electrical system, including wiring, connectors and batteries, for signs of corrosion or damage. Keep batteries charged and clean terminals regularly.
9. Belts and chains
Check belts, chains and drive systems for tension, wear and alignment. Replace any worn or damaged components to prevent unexpected breakdowns.
10. Hydraulic systems
Monitor the level and quality of hydraulic fluid. Check for leaks and replace worn or damaged hoses, seals or hydraulic components as necessary. Make sure hydraulic systems are bled and at proper pressure.
11. Braking and safety systems
Inspect and maintain brake systems regularly, including brake pads, drums, and hydraulic brakes. Make sure all safety features, such as lights, alarms, and emergency stop switches, are in working order.
12. Equipment cleaning
Keep equipment clean and free of dirt, debris and corrosive materials. Regular cleaning can prevent rust and extend the life of components.
13. Operator training
Train equipment operators in the proper and safe use of equipment. Improper use can cause premature wear and damage.
14. Record keeping
Keep detailed records of all maintenance activities, including dates, parts replaced, and any problems found. This documentation helps track equipment history and informs future maintenance needs.
15. Professional service
Schedule regular professional maintenance and inspections by qualified technicians. They can identify potential problems and perform more in-depth maintenance.
16. Storage and shelter
When not in use, store the equipment in a protected location to protect it from adverse weather conditions and exposure to ultraviolet radiation. Use appropriate covers if necessary.
17. Update and modernization
Consider upgrading older equipment with modern technology or components that improve efficiency, safety, and compliance with current regulations.
By following these maintenance tips, you will not only extend the life of your specialty equipment but also improve workplace safety. Regular maintenance is a proactive investment that can save you time and money in the long run by preventing breakdowns and costly repairs.