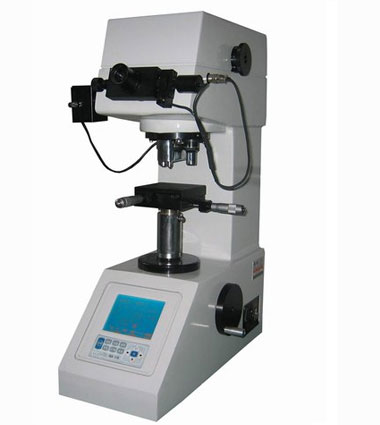
Industrial materials testing equipment: ensuring quality and reliability in manufacturing and construction
Industrial materials testing equipment plays an important role in ensuring the quality, reliability and safety of materials used in manufacturing and construction. From testing machines to hardness testers and non-destructive testing (NDT) equipment, these tools enable engineers and technicians to evaluate the mechanical properties, integrity and performance of materials according to industry standards and regulatory requirements. In this article, we will look at the functions, features, and applications of industrial materials testing equipment, including testing machines, hardness testers, and non-destructive testing equipment.
1. Test machines:
Testing machines, also known as universal testing machines (UTM), are versatile instruments used to perform a variety of mechanical tests on materials, components and products. The main features and benefits of testing machines include:
- Flexibility: Testing machines can perform tensile, compression, bending and torsion testing on a wide range of materials, including metals, plastics, ceramics and composites, allowing for comprehensive material characterization and performance evaluation.{16 }
- Accuracy: Testing machines are equipped with precision load cells, displacement sensors and control systems to ensure accurate
- Customization: Testing machines can be configured with a variety of grips, fixtures and accessories to suit different sample geometries and testing requirements, allowing customized testing solutions for specific applications and industries.
- Safety: Testing machines are designed with safety features such as overload protection, emergency stop buttons and locking mechanisms to ensure operator safety and equipment integrity during testing.
2. Hardness testers:
Hardness testers are specialized instruments used to measure the hardness of materials, which is a key indicator of their mechanical properties and resistance to deformation. Key features and benefits of hardness testers include:
- Versatility: Hardness testers are available in a variety of types, including Rockwell, Brinell, Vickers and Knoop hardness testers, each suitable for different types of materials, surface conditions and testing requirements.
- Accuracy: Hardness testers provide accurate and reliable hardness measurements, allowing engineers to confidently evaluate changes in material hardness, shell depth, and heat treatment effects.
- Portable: Handheld hardness testers are compact, portable devices that allow on-site hardness testing of large or immovable components, providing convenience and flexibility for on-site inspections and quality assurance activities.
- Non-destructive testing: Some hardness testers, such as portable rebound hardness testers (such as Leeb testers), use non-destructive testing techniques to evaluate the hardness of a material without damaging the sample, making them ideal for quick and easy hardness measurements in place.
3. Non-destructive testing (NDT) equipment:
Non-destructive testing (NDT) equipment covers a wide range of inspection methods used to evaluate the integrity, defects and properties of materials and components without causing damage. Main characteristics a
- Safety: Non-destructive testing techniques such as ultrasonic testing (UT), radiographic testing (RT), magnetic particle testing (MT) and eddy current testing (ET) allow for close inspection of material without compromising integrity designs. o
- Detection sensitivity: Non-destructive testing equipment can detect internal and surface defects, discontinuities and anomalies in materials,
- Cost-effective: Non-destructive testing techniques can identify defects and potential failures at an early stage, minimizing the risk of costly repairs, downtime and safety hazards associated with in-service material failures.
- Compliance: Non-destructive testing equipment helps industrial facilities comply with regulatory standards, codes and specifications governing material quality, safety and performance, ensuring compliance with industry best practices and customer requirements.
Conclusion:
Industrial materials testing equipment, including testing machines, hardness testers, and non-destructive testing (NDT) equipment, play a critical role in ensuring the quality, reliability and safety of materials used in manufacturing and construction. Using advanced technology and testing techniques, industrial plants can accurately evaluate material properties, identify defects, and optimize product performance, resulting in improved product quality, durability, and customer satisfaction. As industries continue to prioritize quality, safety and regulatory compliance, implementing innovative materials testing solutions will continue to be essential to achieving excellence in today's competitive marketplace.