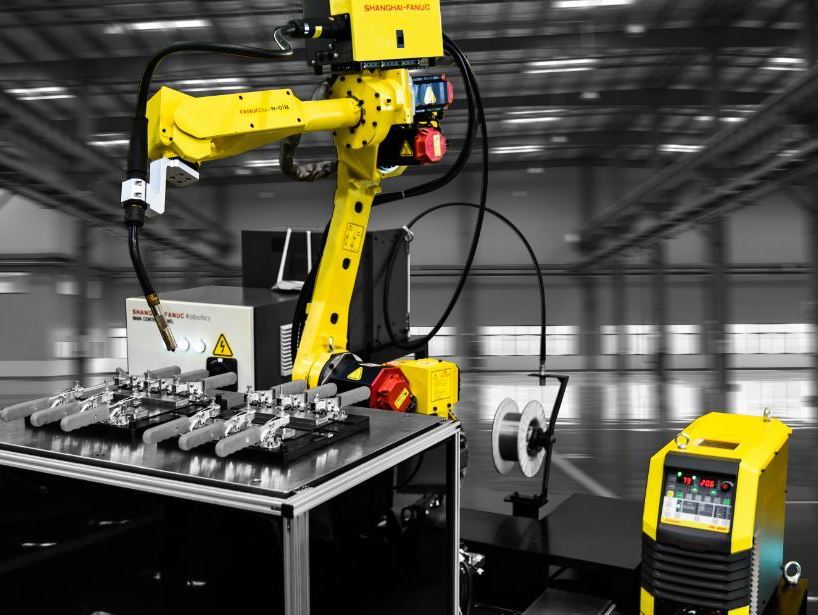
Name: Industrial Welding Equipment: Provides precision joining in metalworking and construction
Introduction: Industrial welding equipment plays a key role in metal fabrication, construction and repair, providing precise joining of metals to create structures, components and assemblies. From arc welders to MIG welders, TIG welders and welding consumables, these tools provide versatility, reliability and efficiency in a variety of industrial environments. In this article, we'll take a closer look at the features, types, and applications of industrial welding equipment, highlighting their importance in producing strong, durable, and high-quality welds.
Features of industrial welding equipment:
- Power and Productivity: Industrial welding equipment provides high output power and productivity for a wide range of welding applications, including the fabrication of thick metal structures and precision welding of thin materials.
- Versatility and Flexibility: The welders offer versatility and flexibility in welding processes, allowing operators to select the most suitable method for specific applications such as shielded metal arc welding (SMAW), gas metal arc welding (GMAW) and arc welding tungsten in a gaseous environment (GTAW).
- Advanced Control and Automation: Many industrial welders are equipped with advanced control systems, automation capabilities and programmable settings to accurately control welding parameters, ensuring consistency, quality and efficiency in welding operations.
- Durability and Reliability: Industrial welding equipment features rugged construction, long-lasting components and advanced cooling systems to withstand harsh operating conditions, intensive use and long-term operation without compromising performance or reliability.
- Safety and User-Friendly Design: Welders are equipped with safety features, ergonomic designs and intuitive controls to enhance operator safety, comfort and productivity when welding, reducing the risk of accidents and injuries.
Types of industrial welding equipment:
- Arc welders: Arc welders, also known as stick welders or SMAW welders, use an electric arc between a consumable electrode and the workpiece to create welds. These machines are versatile, portable and suitable for welding a wide range of metals and thicknesses in construction, fabrication and repair applications.
- MIG (Metal Arc Welding) Welding Machines: MIG welding machines use a continuous solid wire electrode and a shielding gas to produce welds, providing high deposition rates and superior weld quality. They are widely used in the automotive, manufacturing and metal fabrication industries due to their ease of use and versatility.
- TIG (Gas Tungsten Arc) Welding Machines: TIG welding machines use a non-consumable tungsten electrode and inert gas shielding to create precise, clean welds with minimal spatter and distortion. They are preferred for welding thin materials, stainless steel, aluminum and exotic alloys in the aerospace, nuclear and automotive industries.
- Welding Consumables: Welding consumables include electrodes, filler metals, fluxes, and shielding gases used in various welding processes to ensure arc stability, slag removal, and proper melting of metals. Proper selection of consumables is critical to obtaining high-quality welds and maintaining weld integrity in industrial environments.
Application of industrial welding equipment:
- Structured Metal Fabrication: Industrial welding equipment is used in steel fabrication shops to join steel beams, sheets, pipes and sheet metal components in the construction of buildings, bridges and machinery.
- Construction and Infrastructure: Welding machines play a vital role in construction projects involving steel fabrication, concrete reinforcement, and pipe joining, ensuring the structural integrity and durability of buildings, bridges, and infrastructure.
- Automotive Manufacturing: Welding equipment is needed in automobile manufacturing plants to join body panels, chassis components and exhaust systems, ensuring the structural integrity and safety of vehicles.
- Shipbuilding and Marine Engineering: Welding technology is used in shipyards and marine engineering facilities to produce ship hulls, bulkheads, piping systems and offshore structures that meet stringent requirements for strength, corrosion resistance and watertightness.
- Repair and Maintenance: Industrial welding equipment is essential for repairing and maintaining machinery, equipment and infrastructure in industries such as mining, oil and gas and manufacturing, extending the life and functionality of assets.
Conclusion: Industrial welding equipment serves as the backbone of the metalworking, construction and repair industries, providing accurate, efficient and reliable joining of metals in a variety of applications. Whether it's arc welders for heavy-duty manufacturing, MIG welders for automotive assembly lines, or TIG welders for aerospace components, these tools provide the versatility, performance and quality needed to meet the demanding demands of today's industrial applications.