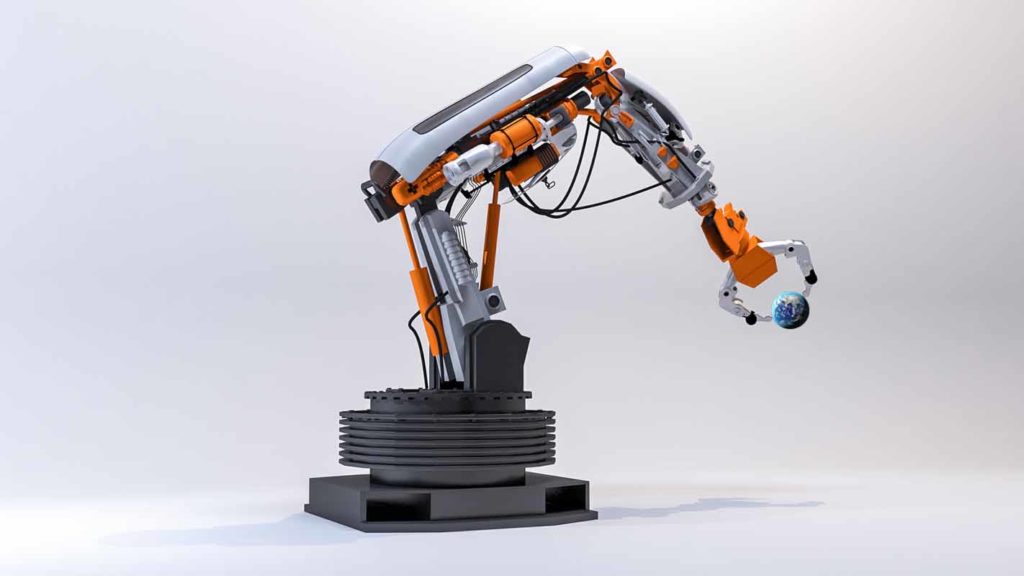
Title: Revolutionizing Industries: The Impact of Industrial Robots
Introduction: In recent years, industrial robots have become indispensable equipment in various sectors, revolutionizing traditional manufacturing, warehousing and logistics processes. From robotic arms to automated guided vehicles (AGVs) to collaborative robots (cobots), these advanced machines are changing the way businesses operate, improving efficiency, accuracy and safety across the board.
Role of Robotic Manipulators: Robotic manipulators, also known as articulated robots, are versatile machines designed to perform a wide range of tasks in industrial settings. Equipped with multiple joints and finite elements, these robotic arms can mimic the dexterity and precision of human hands, making them ideal for tasks such as assembly, welding, painting and material handling. With programmable movements and high repeatability, robotic arms can optimize manufacturing processes, increase throughput, and ensure consistent quality in manufacturing operations.
Automated Guided Vehicles (AGVs): AGVs are autonomous mobile robots designed to transport materials, parts or finished products in industrial facilities. These vehicles travel along predetermined routes using various navigation technologies such as laser guidance, magnetic tape or visual surveillance systems. AGVs can efficiently move heavy loads throughout workshops, warehouses or distribution centers, eliminating the need for manual material handling and reducing labor costs. With advanced safety features and real-time monitoring capabilities, AGVs improve workplace safety and optimize material flow in dynamic industrial environments.
Collaborative Robots (Cobots): Collaborative robots, or cobots, are a new generation of robots designed to work collaboratively with people in shared workspaces. Unlike traditional industrial robots, cobots are equipped with advanced sensors and safety features that enable safe and intuitive human-robot collaboration. Cobots can perform a wide range of tasks, from assembly and packaging to equipment inspection and maintenance, with minimal setup time and programming complexity. By enhancing human capabilities and automating repetitive tasks, cobots improve the productivity, flexibility and ergonomics of manufacturing operations.
Impact on Manufacturing: The integration of industrial robots into manufacturing processes has significantly changed the industry landscape. With robotic automation, manufacturers can achieve higher levels of productivity, accuracy and responsiveness, resulting in lower production costs and greater competitiveness in global markets. Robotic automation also allows manufacturers to quickly adapt to changing market demands, optimize the use of resources, and enhance product quality and customization.
Impact on warehousing and logistics: In warehousing and logistics, industrial robots play a critical role in optimizing operations, managing inventory, and accelerating order fulfillment processes. AGVs automate material handling and transportation, reducing cycle times and minimizing errors in warehouse operations. Robotic arms are used for palletizing, sorting and packaging, increasing throughput and reducing manual labor. By integrating robotics, warehouses and distribution centers can achieve greater levels of efficiency, scalability, and customer responsiveness.
Conclusion: Industrial robots have become an indispensable asset in modern industries, promoting efficiency, innovation and competitiveness in the manufacturing, warehousing and logistics sectors. With the continued advancement of robotics technology and the rise of collaborative automation solutions, businesses can unlock new opportunities for growth, productivity and sustainability in an ever-changing industrial landscape. As robotics continues to advance, the potential for transformative impact on industries around the world remains limitless.